Why meat processing plants infect many employees with COVID-19?
The situation
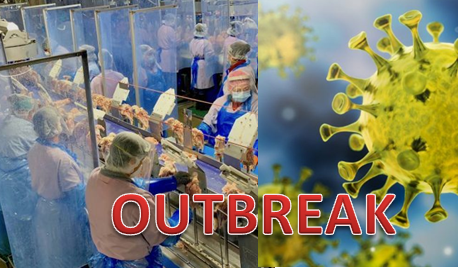
During last month, beef, pork, and poultry processing plants across the US have emerged as dangerous new hot spots for the coronavirus. Many plants have been forced to temporarily stop operations due to very high numbers of cases and fatalities.
According to a CDC report from May 8 4,913 (approximately 3%), of meat and poultry workers in meat plants in 19 states tested positive for the coronavirus as of April 27, with 20 COVID-19 related deaths. In Iowa and South Dakota, 1/5 of the workers in the states’ largest slaughterhouses got sick. In meat processing plants, the percentage of workers diagnosed with COVID-19 ranged from 0.6% to 18.2%.
Smithfield, the nation’s largest pork producer, has reported 783 cases in April, and two deaths in its Sioux Falls, South Dakota plant, which closed on April 14, three weeks after the first worker tested positive. JBS USA, which slaughters almost a ¼ of the nation’s cattle, sent home 6,000 of its workers (with pay) after reporting hundreds of COVID-19 cases. Cargill and Tyson Foods have also been forced to shut some of their facilities following outbreaks.
The phenomenon is not confined to the US. Meat plants worldwide (e.g., Canada, Spain, Germany, the UK, Brazil, Australia, and Ireland), are witnessing the same problem.
What is it about meatpacking plants that increase people’s risks of catching the COVID-19?
According to the CDC’s the main risks to meatpackers are caused by workers being near to each other for prolonged periods of time.
Normally, workers get only seconds to complete their task before the next chunk of meat arrives. As a result meat processing is a demanding, dangerous, labor-intensive job done mainly by underpaid, undocumented workers, and recent immigrants to the US. Many workers live in multigenerational homes or other crowded housing environments. They may also arrive at work by buses operated by the company, riding for a long time each day to and from the plants.
In meat processing plants the temperature of the processing rooms is frigid, and forceful ventilation systems are utilized to prevent the meat from spoiling or getting contaminated with pathogens. These conditions could also contribute to the high rates of infection among processing plant workers. These low temperatures allow the coronavirus to stay for longer periods and linger in droplets, thereby increasing the infection risks.
With many meat plants shut or operating at reduced capacity, pig farmers have to euthanize animals, and the food supply is being harmed. Meanwhile many meat counters are empty.
CDC and OSHA recommendations to the meat industry
The CDC and OSHA issued guidelines to the meat industry that include the configuration of the communal work environments to allow workers to be spaced at least 6′ apart in all directions, if possible. The recommendations include modifying the workstations’ alignment so that workers do not face one another, and practice social distancing during breaks.
Another recommendation is to add physical barriers, such as strip curtains, plexiglass, or other impermeable separators or partitions, to make sure that meat and poultry processing workers are separated from each other.
Hand washing stations or hand sanitizers (with at least 60% alcohol) should be placed in multiple locations to encourage hand hygiene. Break times should be staggered, or create temporary break zones and restrooms to avoid groups of more than 10 workers during breaks. Workers must maintain at least six feet of distance from others at all times, including breaks.
Worker’s arrival and departure times should be staggered to avoid congregations of workers in parking areas, locker rooms, and adjacent to time clocks.
An important recommendation is of wearing masks as a face covering as a protective measure.
The measures taken to stop the COVID-19
Most facilities implemented many changes to comply with the CDC recommendations. For example, JBS USA has implemented these measures at all of its facilities. JBS is also providing surgical masks, which all workers must wear. Fever screening is employed to all employees using hands-free thermometers and thermal imaging before they can enter a facility, and they also hired dedicated staff for additional cleanings.
Some facilities added outdoor break areas to decrease contact between workers. Many companies installed physical (e.g., plexiglass) barriers between workers; however, this was not practical for all worker functions.
Companies had changed personnel policies to allow sick workers to leave without loss of seniority or pay, to enable symptomatic workers to stay home. They are avoiding any incentives that might encourage workers to come to work while being symptomatic. Some companies are offering more generous sick leave.
Why the measures taken so far do not seem to be sufficient
Despite those measures, the virus continued to spread in the facilities, perhaps because the facilities have specific characteristics allowing the coronavirus to spread more quickly. Cold temperatures, overcrowded work conditions, high-speed lines, and long working hours might cause meat plant workers to be much more susceptible to COVID-19.
In Applied and Environmental Microbiology, (May 2010, p. 2712–2717), a study shows that testing of similar viruses had shown that at 4°C infectious virus persisted in droplet’s and on surfaces for as long as 28 days, and inactivation is lowest in dry air (20% RH). Inactivation was more rapid at 20°C than at 4°C at all humidity levels. The virus viability was rapidly lost (>3 log10) at higher temperatures (40 0C) and higher RH.
The low temperatures that exist in the manufacturing plants allow the virus to stay viable outside the human body for a longer time, increasing its survival in the air. It is a significant factor that increases the risk of infection in these plants.
Six feet might not be enough distance to prevent transmission in the fast air movement in the plant, with larger, heavier droplets that are likely to travel farther than 6 feet before falling to the ground. Therefore, fast breathing workers might shed virus across longer distances.
What could be making the situation worst is a high number of asymptomatic workers. Wired reported that when a pork processing plant in Missouri (with the state health department) tested its workforce, more than 730 workers tested positive. All of them were asymptomatic. These employees had no fever, and they could have been spreading the virus for a couple of weeks.
The situation in the meat facilities is not simple to resolve. It might take either the availability of a vaccine or herd immunity to stop the spreading in the plants. Innovative solutions are required to minimize the problem. Until then, production needs to continue with the best mitigating practices.
One response to “Why meat processing plants infect many employees with COVID-19?”
In the US, meat processing facilities are characterized by cramped, loud, frigid conditions allowing the coronavirus to stay alive and jump from person to person. In Denmark (Danish Crown’s Horsens facility), robots are used in their pig slaughterhouses. The robots can help keep workers safe and meat plants running. @ https://www.wired.com/story/covid-19-makes-the-case-for-more-meatpacking-robots/amp