What design is your Quality System? Is it a reactive and inspection-based design or is it a proactive risk-based prevention design?
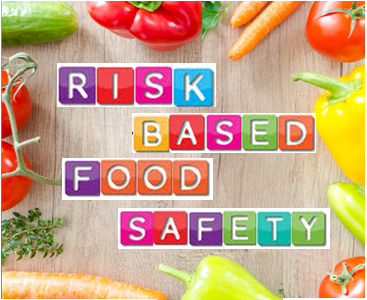
We see daily examples of significant product failures in consumer’s hands. We’ve all seen these stats. The FDA estimates 48 million cases of foodborne illnesses annually—sickening 1 in 6, 128,000 hospitalizations and 3,000 American deaths annually. Since the start of 2014, there have been more than 100 million vehicles recalled in the United States. That number is just shy of half of all vehicles on the road today. Are these results acceptable? I don’t think so, in fact, I believe these results are clear evidence that our quality systems are failing!
Steve Gruler
So where are the demands for change and overhaul of our product safety and quality systems?
Since the beginning of time, the foundation of product quality systems is rooted in an inspect and reject philosophy. I have had the pleasure and honor to work for numerous outstanding companies around the globe. From the small Mom and Pop companies to the world’s largest organizations. My experience shows an overwhelming majority of companies embrace a reactive inspection- based philosophy. In many cases, these systems are certified to global standards. And yet we still see crippling product failures around the world.
Good news is we have seen an increased interest around a preventative approach to product quality and safety. Many agree this is a right approach and is needed. My concern is, very few organizations have taken action and implemented a preventative risk-based quality system. I know, for those that have, they are experiencing phenomenal results; significant reductions in waste, rework, hold orders, field failures and recalls.
Even amidst significant brand, devastating recalls and increased awareness for moving towards a proactive/preventative philosophy we still fall short of this approach grabbing hold. The most observable example is the Food Safety Moderation Act of 2011. It proclaims prevention.
For the first time, FDA will have a legislative mandate to require comprehensive, science-based preventive controls across the food supply. A welcomed approach, however as you dig into the details, the mandate severely depends on audits and inspections.
FSMA establishes a mandated inspection frequency, based on risk, for food facilities and requires the frequency of inspection to increase immediately. All high-risk domestic facilities must be inspected within five years of enactment and no less than every three years thereafter. Within one year of enactment, the law directs FDA to inspect at least 600 foreign facilities and double those inspections every year for the next five years.
This is not a proactive/ preventative approach, it is clearly a prioritized inspection approach based on risk. I think the FDA has taken a good step forward with FSMA and I have witnessed some improvements due to the new act. My concern is that manufacturer’s will focus more on meeting regulations than delivering superior low-performance risk products via predictive risk mitigation quality systems.
The dictionary definition of Preventive is: designed to keep something undesirable such as illness, harm, or accidents from occurring.
What does a risk-based preventative quality system look like? One core piece, you must be able to effectively predict issues in-order to prevent it from becoming a crisis.
To name just a few, its element includes:
- Clearly defined risk-based product standards
- Determined product performance levels (anticipated field failure rates).
- Enterprise-wide transparent performance metrics (provides a clear confident view of product performance). Everyone has a direct line of sight and manages with the same performance risk data, (from the shop floor to the board room).
- A developed culture of identifying, mitigating and managing product risk to the brand
- Well defined quality roles and responsibilities for all functions.
- Applied throughout the entire supply chain.
- A risk based continuous improvement process
This is just a flavor of what a preventive system would include.
I would welcome your thoughts, comments, and recommendations. Please contact me at sgruler@gqc-inc.com https://www.linkedin.com/in/steve-gruler
Steve Gruler, Founder & CEO GQC